どもイッシぃ~です。
製造業界で化学プラントで働くことを検討している方
なんだか化学プラントって危険なイメージがありますよね?
V-500x333.jpg)
はい、大正解だと思います。
ただ、実際の危険性についてはリアルに想像することは難しいかと思います。
そこで今回は、化学プラントで働く上のでのリスク(危険性)について、リスクの内容とその理由について語りたいと思います。
この記事を読めば
一般的な製造業と異なる化学プラント特有のリスクをイメージできるかと思います。
リスクを正しく知ることは、安全を確保するうえで必要不可欠です。
これから、化学プラントで働こうと思う方は、この記事を参考に頂けたら幸いです。
■この記事の信頼性について
東証一部上場企業の石油化学コンビナート(化学プラント)で生産技術スタッフとして約4年勤務していた実体験より回想を交えて記載しています(2005年~2009年)。
それでは、どうぞご覧下さい。
化学プラントで働くリスク
石油化学プラントの仕事と言っても、企業の規模や形態によりその中身は多彩です。
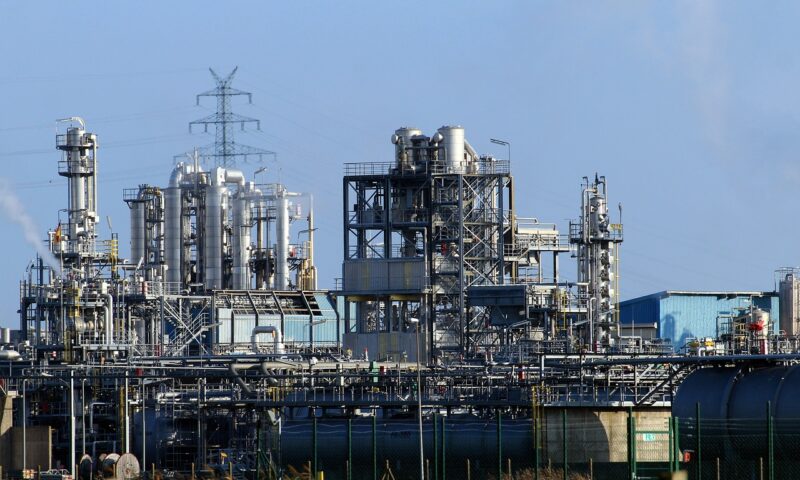
扱うもの、どんな素材を製造するかによりプロセスは異なりますが
一般の製造業にくらべ基本的なリスクが高いことを認識するべきですね。
では、その理由について。
化学プラント特有のリスク
主なリスクは以下のイメージで、特に赤字の項目がヤバいです。
■物理的リスク
爆発事故、墜落、挟まれ、殴打、転倒、切傷などなど
■毒性リスク
有害性物質の暴露・吸引、失明、窒息、発がん率UP
■その他リスク
熱傷、冷傷、感電など
リスクが高いのは何故?
化学プラントでは、複数の物質を「化学反応」させて意図する素材を生成させています。
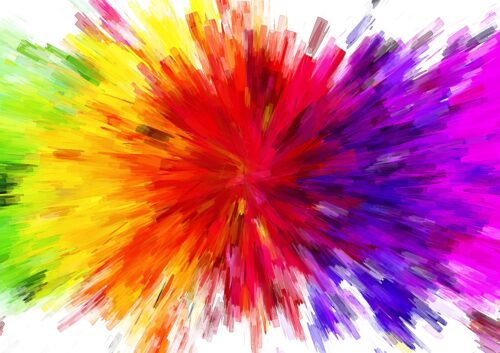
まずはエネルギーの面から考えてみましょう。
高エネルギーの取り扱いが多い
「化学反応」をさせる為には、エネルギーが必要ですし、また「化学反応」させることにより、発熱といったエネルギーの上昇プロセスが多いのが特徴です。
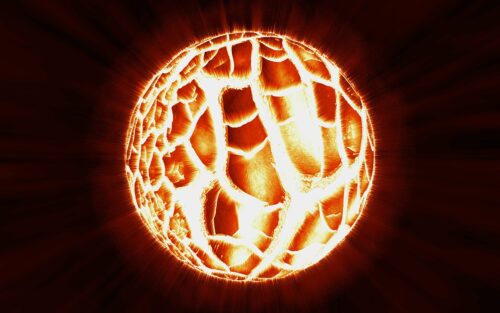
そして「プラント」と言うだけあり、とても規模が大きい環境であるので必然的に取り扱うエネルギーも「多い(大きい)」ということになります。
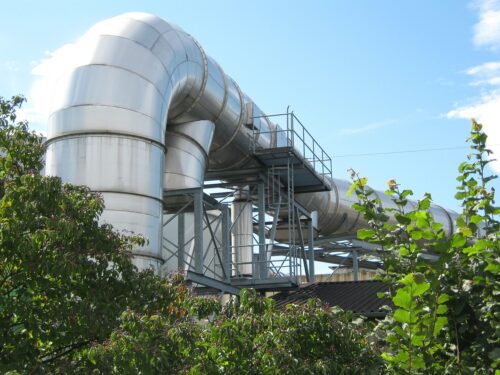
つまり、化学プラントでは「高温・高圧」という状態を、量的にも大量に取り扱っているのがの一般的な姿でしょう。
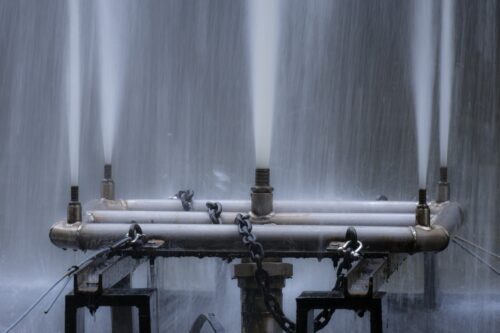
【取り扱いするエネルギー】
「高温・高圧」x 大量 = エネルギー総量(密度)が高い = より危険
何か問題が起きた時、エネルギーが低ければ大したことはないのですが、化学プラントでは、至る所で「高」エネルギーを「貯蔵」「移送」「使用」「取り出し」「変換」と様々なプロセスで取り扱っているので必然的に危険性も高まるワケですね。
更には、規模の大きさ故に管理の問題も出てきます。
大規模で完全な設備管理が困難
充分な設備管理をしていないと事故が発生し易くなります。
ですが、充分な設備管理が難しい側面があることを知っていただきましょう。
化学プラントの敷地は膨大な広さで、敷地全体は車を使っても数分かかる程です。
当然、個々のプラントの大きさも相当なものです。
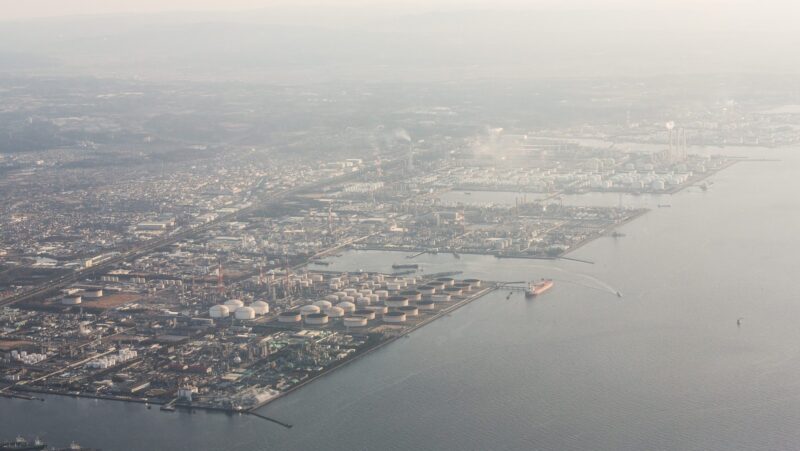
プラント内の設備も多ければ、プラント間を繋ぐ配管も無数にありますし
そして質が悪いのが、目で追えない配置であることが殆どという事ですね。
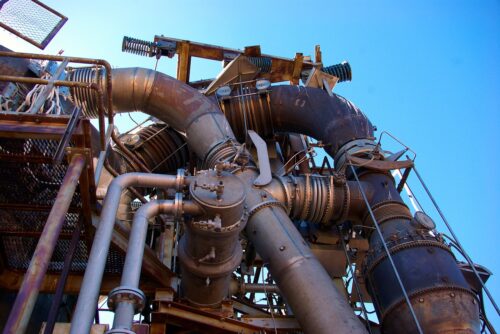
例えば、Aの物質が流れる配管(配管Aとしましょう)があるとしましょう。
これを目で追っていると、途中で他の配管とクロスしていて、最終的に配管Aと思っていたら配管Bだったというケースは珍しいことではありません。
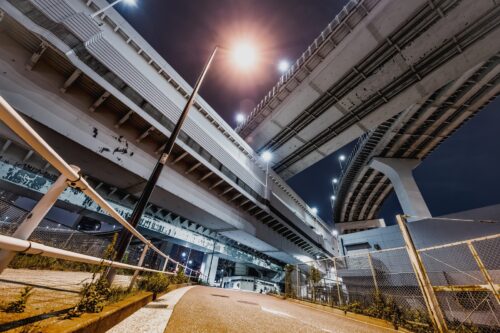
一つの反応設備にコネクトする配管も十数種類ありますので、プラント内には数百本の配管がひしめき合っています。
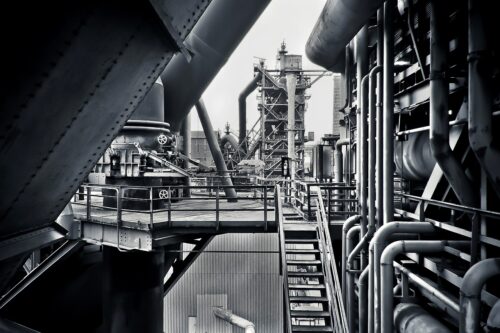
配管だけでも吐くほど多いのですから、反応設備を含めれば気が遠くなる様な管理対象があるワケです。
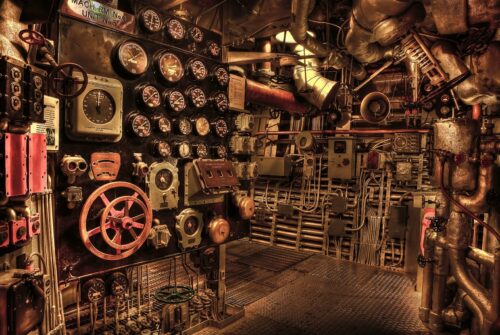
【管理の難しさ】
膨大な広さ x 膨大な数 x 不可視箇所の多さ = 完全な管理は困難 = 危険
ちなみに、目で直接見られないパターンは、設備の物陰になっている場合の他、「地中に埋まっている」という極悪な場合もあります(笑)
だからと言って無管理ではなく、大枠の定期修繕工事で計画的に補修を行う他、日常のプラントステータスを集中制御監視システムでモニタリングし、異常が発生していると判断したら現地現物を確認するといった繰り返しで対応していました。
いずれにせよ予防保全は厳しく、予知保全(兆候があれば対応)か事後保全(問題が発生したら対応)が精一杯なのです。
人為的エラーによる事故
いわゆるヒューマンエラーですが、化学プラントではちょっとしたエラーでも大事故に繋がる恐ろしさがあります。
一般的な製造業では、誤操作ができない仕組み「フールプルーフ」での設計が多いかと思いますが化学プラントでは危険操作や間違った操作が簡単にできてしまうのです。
現場には無数の配管、無数の操作バルブやボタンがあり、その操作も自動ではなく手動で行う作業も少なくありません。
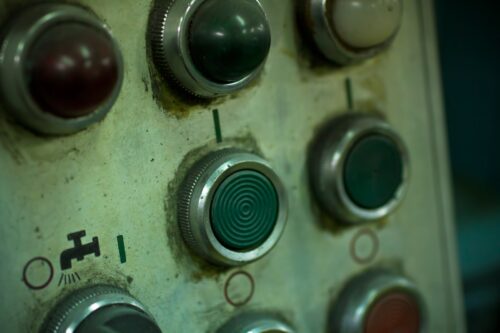
例えば、ガスが封入されているタンクの元バルブとか、大気解放するフタのボルトを緩めたりなどがありますが、この作業の多くはコスト的に手作業での実施となります。
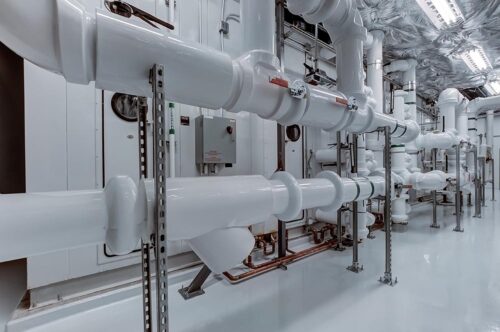
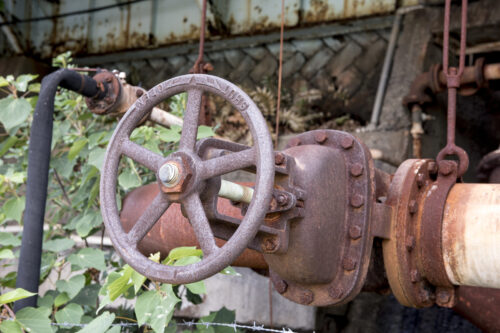
もちろん、動力的にはエアーやモーターの力で駆動させたりもしますが、その指示はマニュアルモードで行う場合も同じです。
似た様な配管(材質、位置、色、直径)、似た様なタンクが乱立する環境ですので、前後の配管の繋がりの関係を確認を含め、操作対象を確信してからの操作が必須となりますが、やはり「見間違い」や「思い込み」をしてしまう恐れが高いのです。
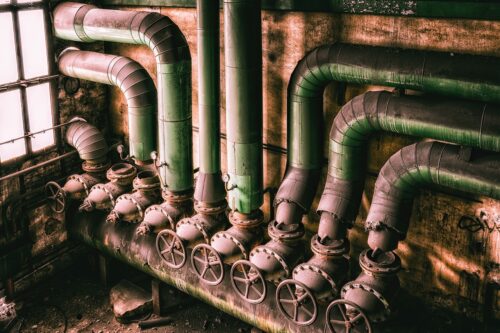
その事例を少し語ってみます。
■私のエラー実体験より
現場実習でのこと。
重合缶が4つ並んだエリアで、反応が終了した重合缶③を解放しようとマンホールのボルトを緩めていたら、プシューッ!!っと凄まじいガス漏れの様な音が!?
何か変な感じがすると思いながらも、「気のせいかな」とボルトを緩めているとその音はどんどん大きくなる一方。
流石にオカシイと思い、監視室に戻って作業工程を確認すると・・・
なんと、私が解放しようとしていたのは「反応中」の重合缶②のマンホールでした。
そのまま、ボルトを緩め続けていたらどうなっていたことやら・・・いや、死んでいたでしょうね。
慌てて、間違えて開けようとしていたマンホールのボルトを締め直し、本来の重合缶③のマンホールを開けましたが、思い出すだけでも恐ろしいことをやってしまったというか
・・・故意でなくても「やれてしまう」のです。
当時の教育担当の班長さんに
おい、えらい時間掛かったみたいやけどどうしたんや?
と声掛けされ
「いや・・・ちょっと、・・・なんでもないです大丈夫です」と返事をしながらも、心臓がバクバクと別の反応をしていた記憶が鮮明です(笑)
取り扱い物質の有害性
高エネルギー他、取り扱いする物質の有害性が高いことも注意すべきことですね。
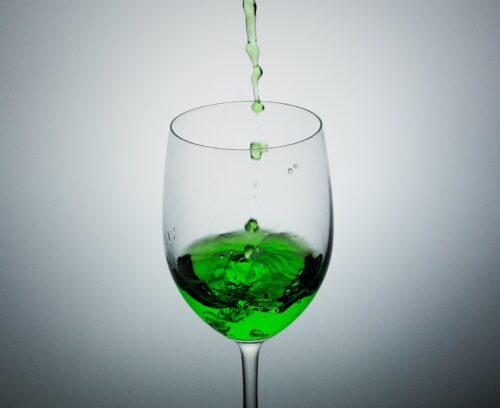
素材の主原料となる物質の他、反応を開始させる「触媒」、反応を安定化させる「助剤」など手作業で取り扱う事も多々あります。
ゴーグル、防毒マスク、手袋などの保護具を着用をしていれば万全という単純なものでもありません。毒性が高い物質の他、衝撃や温度上昇で爆発の危険性がある危険物第5類(自己反応性物質)の取り扱いも実際に行っていました。
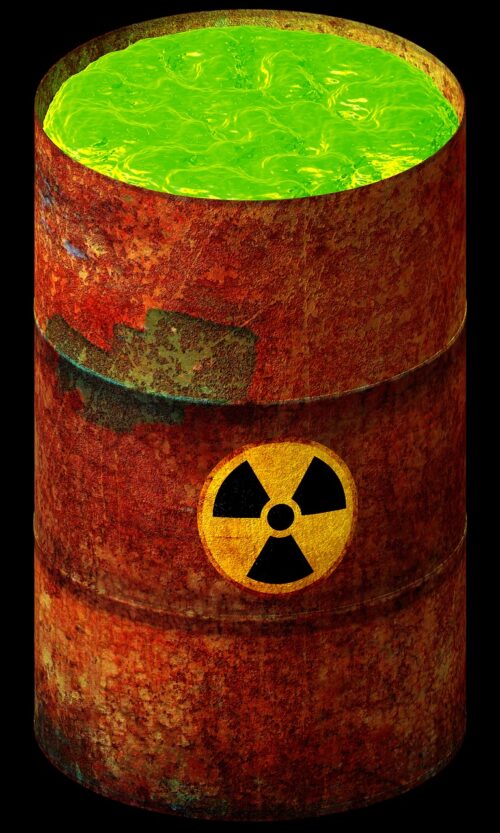
もちろん、危険物第5類は常温保管ではなく冷蔵保管していたハズですが、停電時などどうしていたか記憶がありません(笑)
墜落・転落リスク
化学プラントには、高所かつ足場が不安定なスポットでの作業が少なくありません。
例えば、サイロなんかがそうですね。
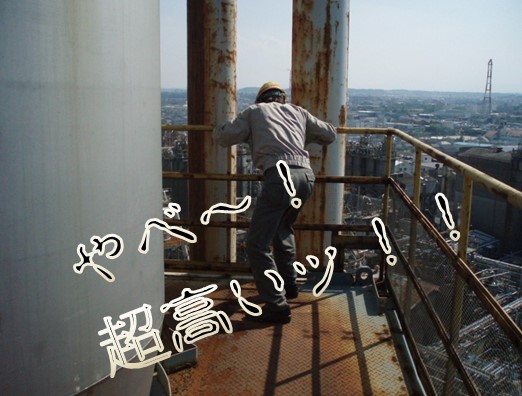
サイロの高さはざっと30~40mあったりします。
これぐらいの高度ですと、結構な風が吹き荒れているものです。
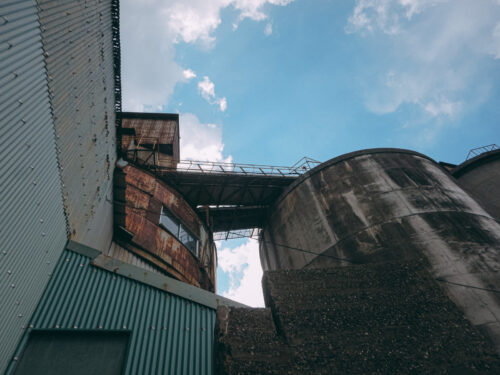
まだサイロの上などは、足場が平たんで「安全帯」を掛ける手摺があるのですが・・・サイロの上部に移動するまでの「螺旋階段」を通る際は結構な恐怖があります。
なにせ、階段には「隙間」がふんだんにあり、下界の景色が「丸見え」なので恐怖には事足りません。
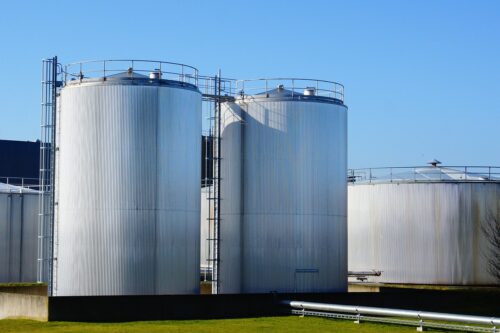
そして、最も恐怖なのは「球状のタンク」。

足場が曲面なので、恐怖のグラフも2次曲線を描きます(笑)
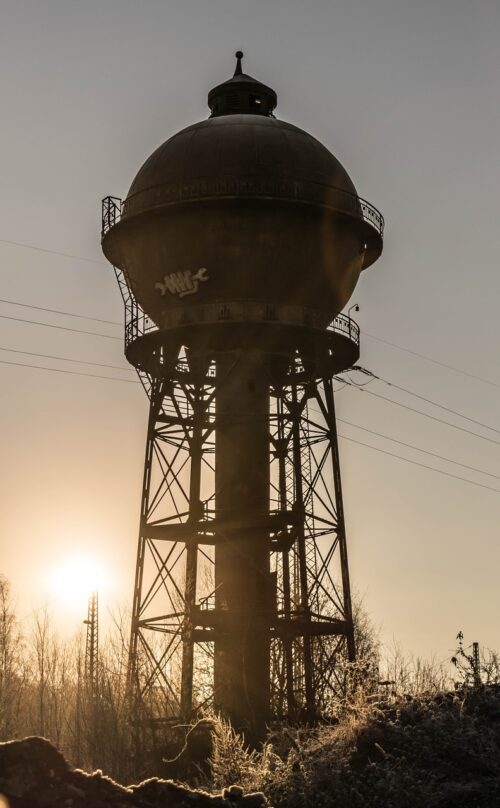
まとめ
如何でしたか?
別にどうってことないじゃん?と思われるかも知れません。
化学プラントのリスクとして一番高いのは、やはり「化学反応」をメインに行っていることだと思います。
高エネルギーの取り扱いをするうえでは、注意すべきことが沢山ありますが
「監視」「設備管理」「オペレーションミス」「不測時の対応」について一つ一つポイントを押さえていくことが重要だと思います。
またコンビナートの規模の他、「設備の設立年度」も考慮に入れるべきでしょう。古いコンビナートですと、毎日の様に設備に不具合が生じてきます。
私がいたプラントでは50~60年の月日が流れていて、突発で起こる設備面の不具合対応にはトコトン苦労しました。
どうせ働くなら新しいプラントを強くお勧めします。
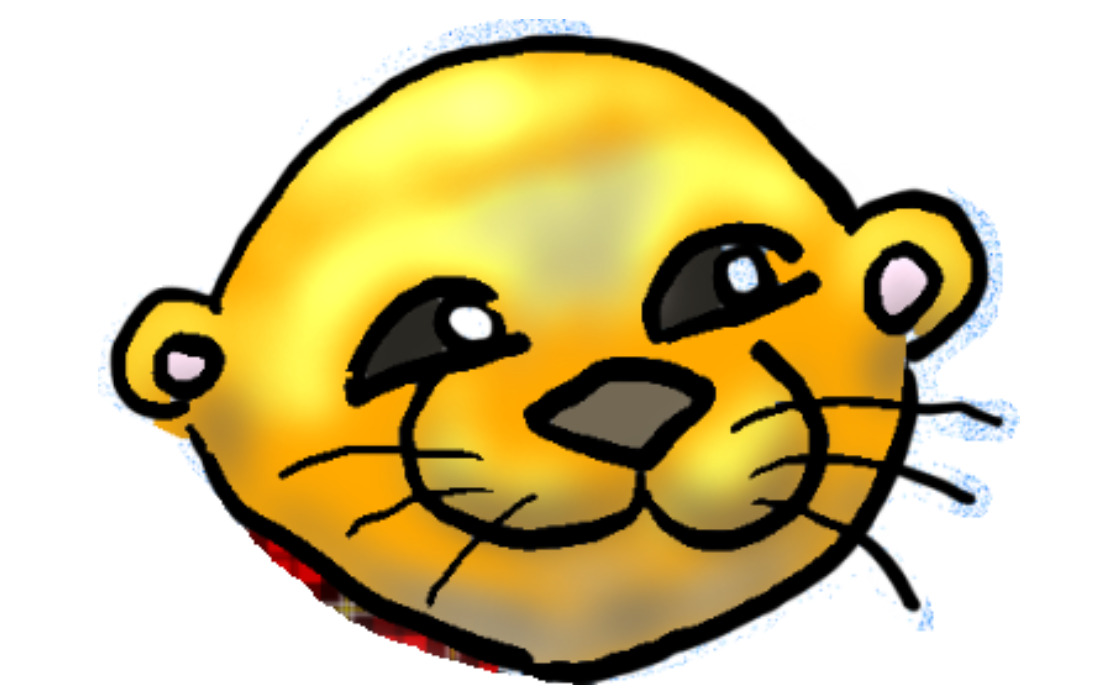
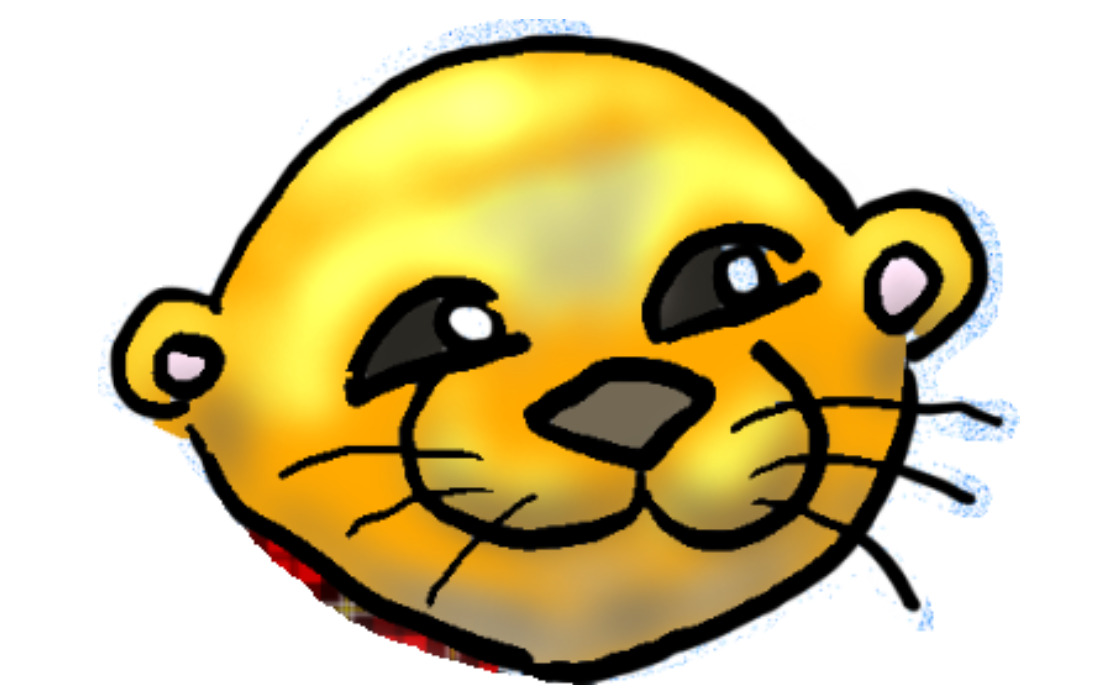
最新記事 by イッシぃ~ (全て見る)
- 財布を落として改めて気付いたこと in 出光 関ケ原SS - 2021年11月17日
- ハッタリは誰得にもならない。中身で勝負するべき2つの理由。 - 2021年10月13日
- どんな理不尽や不可抗力にも負けない最強の思考方法《後編》 - 2021年10月10日
コメント